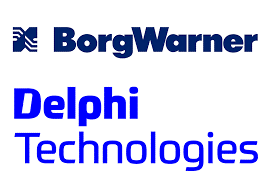
Top Global Battery Management System Industry Trends and Competitive Analysis in 2024; Spherical Insights and Consulting
RELEASE DATE: Dec 2023 Author: Spherical InsightsRequest Free Sample Speak to Analyst
Industry Overview:
Battery management system (BMS) technology is devoted to the supervision of a battery pack, which is an assembly of battery cells electrically arranged in a row x column matrix configuration to enable delivery of a targeted range of voltage and current for a period of time against expected load scenarios. The intelligent part that keeps an eye on and manages any lithium-ion battery pack is called a Battery Management System (BMS). It serves as the battery's brain and is crucial to its longevity, performance, safety, and charge rates. A battery pack is an assembly of battery cells electrically arranged in a row x column matrix configuration to enable the delivery of a targeted range of voltage and current for a duration of time against anticipated load scenarios. Battery management systems, or BMSs, are technologies devoted to the supervision of battery packs. The temperature and voltage levels of the battery cells are constantly being monitored by the BMS. By doing this, user can make sure that every cell functions in unison and avoid any imbalances or variations that can impair battery performance. By maximizing the battery pack's efficiency, this proactive monitoring enables it to provide steady power production for the duration of its life.
Market Statistics Analysis
Global Battery Management System Market Size Insights Forecasts to 2032
- The Global Battery Management System Market Size was valued at USD 7.9 Billion in 2022.
- The Market Size is Growing at a CAGR of 19.8% from 2022 to 2032
- The Worldwide Battery Management System Market Size is expected to reach USD 48.4 Billion by 2032
- Asia Pacific is expected To Grow the fastest during the forecast period
Working of BMS
The main responsibility of a battery management system (BMS) is to ensure the safe and efficient operation of batteries by monitoring and controlling various elements such as voltage, current, temperature, and state of charge. The BMS corrects any parameter that goes above the safe operating range to avoid damage or safety risks. To avoid harm, the BMS may, for instance, lower the charging current if it notices that the battery is getting too charged. In a similar vein, the BMS can turn on cooling systems if the battery starts to overheat. The various components that make up a BMS cooperate to regulate the battery's performance. Among these components are sensors, communication interfaces, microcontrollers, and control circuits.
- Microcontroller: The microcontroller is the main processing unit of the BMS. It collects information from multiple sensors and uses that information to determine how best to regulate the battery's operation.
- Display: A display that shows current battery performance data, like temperature and charge level, is a feature of several BMS systems.
- Sensors: The majority of the battery's parameters, such as voltage, current, temperature, and charge level, are tracked by sensors. These sensors provide the data that the microcontroller needs to decide how to operate the battery.
- Alarm and Safety Features: Alarms and safety features in BMS systems can notify users of possible battery problems, such as overcharging or overheating. These characteristics can lessen the chance of accidents and increase battery life.
- Battery Balancer: Battery balancers assist in making sure that the charging and discharging of each cell in a battery pack occurs in a balanced manner. Harm can be avoided and the battery's lifespan can be extended by doing this.
- Communications Interface: The communications interface allows BMS to communicate with a wide range of other devices, such as the onboard computer of a car. Important diagnostic information about the state and operation of the battery can be obtained through this interface.
- Switches: Switches control the quantity of electricity that flows to and from the battery. They can be used in an emergency or in the event of a malfunction to disconnect the batteries.
Together, these components comprise a comprehensive system that ensures the battery operates safely and effectively by monitoring and maintaining its performance.
BMS design elements are numerous, but two crucial ones are capacity management and battery pack protection management. The two main areas of battery pack protection management are thermal protection, which uses passive and/or active temperature regulation to keep the pack within its safe operation area (SOA), and electrical protection, which means preventing harm to the battery from usage beyond its SOA.
Electrical Management Protection: Current
Electrical safety is achieved by keeping an eye on battery pack current and cell or module voltages. Any battery cell's electrical SOA is limited by voltage and current. A well-designed BMS will preserve the pack by prohibiting operating outside of the manufacturer's cell ratings, which depicts a typical SOA for a lithium-ion cell. To extend battery lifespan, further derating is frequently used to stay inside the SOA safe zone. When charging or discharging, lithium-ion batteries have differing current limitations, though both modes can withstand larger peak currents for brief periods. In addition to peak charging and discharging current restrictions, battery cell manufacturers typically give maximum continuous charging and discharging current limits. A maximum continuous current will undoubtedly be applied by a BMS that offers current protection. To compensate for an unexpected shift in the load conditions, such as the rapid acceleration of an electric car, this could, nevertheless, come before. Peak current monitoring can be implemented by a BMS by integrating the current and, after delta time, choosing to either cut down on available current or completely stop the pack current. This enables the BMS to be both forgiving of high peak demands, provided they are not excessive for an extended period, and nearly immediate sensitive to severe current peaks, such as a short-circuit condition that has not triggered any resident fuses.
Electrical Management Protection: Voltage
Within a specific voltage range, a lithium-ion cell can only function. The inherent chemistry of the chosen lithium-ion cell and the cells' current temperature will ultimately define these SOA bounds. These SOA voltage restrictions are typically further limited to maximize battery lifespan because any battery pack sees a large amount of current cycling, discharge owing to load demands, and charging from a variety of energy sources. The BMS needs to be aware of these boundaries since it will make judgments depending on how close these thresholds are. For instance, a BMS may ask for a gradual reduction in the charging current as it approaches the high voltage limit or, if the limit is achieved, a request for the charging current to be completely stopped. To avoid control, talk about the shutdown threshold, this restriction is typically complemented by extra intrinsic voltage hysteresis considerations. On the other side, a BMS will ask important active offending loads to lower their current needs when they get close to the low voltage limit. This can be accomplished in the case of an electric vehicle by lowering the traction motor's permitted torque. Naturally, to prevent irreversible damage to the battery pack, the BMS must prioritize the driver's safety above all else.
Thermal Management Protection: Temperature
Lithium-ion batteries seem to have a broad temperature operating range on the surface, however, at low temperatures, chemical reaction rates noticeably slow down, reducing the overall battery capacity. They do function significantly better at low temperatures than lead-acid or NiMh batteries, but temperature control is still prudently necessary because charging below 0 °C (32 °F) might be physically troublesome. When charging below freezing temperatures, the anode may experience the phenomena of metallic lithium plating. This is irreversible damage that not only reduces capacity but also makes cells more prone to malfunction in the event of vibration or other stressful situations. By heating and cooling the battery pack, a BMS can regulate its temperature. The size, cost, and performance goals of the battery pack, as well as the design specifications of the BMS and product unit which may take the desired geographic region (e.g., Alaska versus Hawaii) into account all play a role in realized thermal management. Whichever kind of heater you have, it is usually more efficient to use an external AC power supply or a backup resident battery to run the heater when necessary. On the other hand, the main battery pack's energy can be extracted and used by the electric heater to heat itself if its current draw is low. The coolant that is pumped and dispersed throughout the pack assembly is heated by an electric heater if a thermal-hydraulic system is utilized.
Capacity Management
Undoubtedly, optimizing a battery pack's capacity is among the most essential battery performance functions a BMS offers. Ignoring this maintenance could eventually cause a battery pack to lose its usefulness. The main cause of the problem is that a battery pack's "stack," or sequential arrangement of cells, is inherently slightly different in terms of leakage or self-discharge rates and is therefore not quite equal. Although it may be statistically affected by minute differences in the production process, leakage is a property of battery chemistry rather than a flaw caused by the manufacturer. A battery pack may contain well-matched cells at first, but as time goes on, factors like charge/discharge cycling, high temperatures, and normal calendar aging affect how similar cells are to one another in addition to self-discharge. The overall pack voltage is determined by the battery pack's series cell array, and while trying to charge any stack, a discrepancy between nearby cells can cause problems. Every cell in a perfectly balanced set will charge equally, and when the higher 4.0 voltage cut-off level is reached, the charging current can be stopped. The top cell will, however, reach its charge limit sooner in the unbalanced case, necessitating the termination of the leg's charging current before the other underlying cells have reached their full capacity.
Types of BMS
To fulfill its primary command to "take care of the battery," battery management systems can be as basic or as complex as they want, incorporating a broad variety of technologies. On the other hand, these systems can be divided into groups according to their topology, which is related to the way they are set up and function on the various modules or cells that make up the battery pack.
Centralized:
An energy storage system is referred to as centralized when every battery in the system is connected to a single BMS controller that oversees and regulates the entire battery pack. This type of BMS is frequently utilized in large-scale energy storage systems, such as those found in electric automobiles and power grids. Centralized BMS are typically less expensive than spread BMS since they require fewer sensors and communication links. The centralized design may have a single point of failure due to the wiring's potential complexity. The ability to offer a thorough picture of the battery pack and facilitate efficient control and administration of the complete system is one of the primary benefits of a centralized battery management system.
Modular:
The BMS is split up into multiple identical modules, each with its own set of cables, and connects to a specific area of a battery stack next to it, much like a centralized implementation. These BMS submodules might occasionally be supervised by a principal BMS module, whose job is to keep an eye on the submodules' status and interact with external devices. Duplicate modularity makes maintenance and troubleshooting simpler, and it's easy to extend to larger battery packs. The drawbacks include slightly higher total expenses and, depending on the application, the possibility of redundant or underutilized capabilities.
Distributed:
When every battery cell management system or module has its own BMS controller, which communicates with a master controller to operate the entire system, the system is referred to as a distributed BMS. Smaller-scale energy storage systems, such as those in electric cars or home energy storage systems, commonly use this type of BMS. Dispersed battery management systems (BMS) are recognized to be more adaptable and scalable than centralized BMS because of how easily they can be adjusted to changes or additions to the battery system. Furthermore, a distributed BMS can provide redundancy and fault tolerance because each cell or module has its own BMS controller. On the other hand, sensors and communication interfaces may come with more expensive and intricate wiring. The choice between a distributed and centralized battery management system (BMS) is influenced by several factors, such as the size and overall complexity of the battery system, the required level of redundancy and fault tolerance, the cost, and the wiring complexity limitations. Selecting the optimal battery management system (BMS) for a certain application is essential if you want to improve battery longevity, performance, and safety, among other advantages.
Primary/Subordinate:
Though conceptually comparable to the modular architecture, in this instance, the master is devoted to processing and control in addition to external communication, and the slaves are more limited to just relaying measurement data. Therefore, similar to the modular types, the expenses might be cheaper because the slaves' functionality is typically simpler, meaning there is probably less overhead and fewer features that aren't used.
BMS for Electric Vehicles (EV)
An electrical device that is frequently referred to as a "Battery Management System," or BMS, is essential for tracking and managing the performance of EV batteries. It regulates temperature, voltage, and charge level three vital factors for the secure operation of batteries frequently used in electric vehicles. When it comes to batteries used in electric vehicles, lithium-ion batteries are the most preferred type because of their high-power density, low self-discharge, and affordable price. Nevertheless, creating an electric car using a lithium battery carries several safety dangers in addition to its benefits. Because lithium-ion batteries can malfunction and even catch fire in uncommon circumstances for a variety of causes, including age, wear, thermal runaway, and overcharging or over discharging. To deliver safer e-mobility, this forces Automakers & OEMs to implement efficient Battery Management Solutions (BMS) to guarantee EV batteries are within ideal safety limits. A battery in an electric car combines multiple modules, each made up of a group of individual cells. Because each cell in each module tends to charge and discharge at a different pace, it is difficult to monitor battery pack performance. Furthermore, the factors of energy, health, and temperature all affect how each cell behaves. Therefore, for safer and more effective functioning, each battery cell needs to be independently observed. This is where the BMS comes into play; it monitors the parameters regularly and takes quick corrective action if it finds any irregularities. By ensuring the battery operates safely and dependably, this examination provides customers with an electric car that is both effective and secure.
Battery Management Systems in EV come in two varieties: distributed and centralized.
The cost-effectiveness of a centralized BMS lies in its single control unit overseeing all cells; nonetheless, in the event of a control unit malfunction, the entire system is vulnerable to complete failure. In contrast, in a distributed BMS, several control units are commissioned to improve system resilience. This now entails higher expenses and complexity. Automobile manufacturers select the BMS system that best suits their needs and specifications; cost tends to favor centralized BMSs, while reliability favors distributed BMSs.
As demonstrated by the following guidelines, the Battery Management System (BMS) is essential to the operation of electric vehicles in multiple ways.
- Cell Monitoring
- Thermal Management
- Cell Balancing
- Battery Optimization
Benefits of BMS
Depending on the application, a complete battery energy storage system, or BESS, may consist of tens, hundreds, or even thousands of lithium-ion cells arranged strategically. With pack supply currents ranging up to 300A or higher, these systems may have a voltage rating of less than 100V or as high as 800V. Any misuse of a high-voltage pack has the potential to unleash a devastating, potentially fatal event. Therefore, to guarantee safe operation, BMSs are vital.
Functional Safety
This is especially wise and necessary for large format lithium-ion battery packs, without a doubt. However, even smaller formats like those found in laptops, for example have been known to catch fire and do significant harm. Errors in battery management are rare in goods involving lithium-ion batteries since they compromise consumers' personal safety.
Cost and Warranty Reduction
Batteries are costly and sometimes dangerous, and adding a BMS to a BESS raises expenses. More BMS control is required as the system is more complex since higher safety criteria go hand in hand with greater system complexity. However, a BMS's protection and preventive maintenance with regard to functional safety, longevity and dependability, performance and range, diagnostics, etc., ensures that it will save total expenditures, including warranty-related ones.
Life Span and Reliability
The electrical and thermal protection management of the battery pack makes sure that every cell is used in accordance with the stated SOA specifications. This careful attention to detail guarantees that the cells are protected from harsh use and rapid cycles of charging and discharging, which will ultimately lead to a robust system that may offer many years of dependable service.
Diagnostics, Data Collection, and External Communication
Continuous monitoring of all battery cells is one of the oversight jobs. Data recording can be used alone for diagnostics, but it is frequently utilized in conjunction with other computations to estimate the state of charge (SOC) of every cell in the assembly. While some of this data is used in balancing algorithms, it can also be used to tell external devices and displays about the battery pack's health, predict range or range/lifetime depending on current usage, and indicate the amount of energy available.
Performance and Range
Optimal battery capacity can be achieved by BMS battery pack capacity management, which uses cell-to-cell balancing to equalize the SOC of nearby cells across the pack assembly. A battery pack could eventually become worthless without this BMS capability to take into account changes in self-discharge, charge/discharge cycling, temperature impacts, and general aging.
Benefits of BMS for EV
BMS offers a number of noteworthy benefits for electric vehicles.
Performance Optimization
With automated processes to address abnormalities and battery malfunctions, BMS assists in maximizing the performance of the battery packs to increase driving range and battery longevity.
Real-time Data and Diagnostics
Real-time battery observation, data recording for logs on battery health, and defect identification are all done by BMS. This assists OEMs in planning preventative maintenance to address problems and greatly improve customer happiness.
Safety and Reliability
Complete monitoring and safety features for overcharging, draining, and unexpected temperature fluctuations are included in BMS. This guarantees a battery's longevity and safety, reducing the likelihood of mishaps or battery failures for EV owners.
Battery Maintenance and BMS
Routine maintenance is necessary to preserve the battery's longevity even though the BMS is intended to keep it operating correctly. A battery needs to be kept dry and clean, shielded from extreme heat, and neither overcharged or depleted in order to be maintained correctly. The BMS can also assist with battery maintenance by giving information on the battery's performance and alerting the user to any issues that need to be addressed.
Trends of BMS
In order to improve their BMS capabilities and expand their line of automobiles, automakers continuously experiment. Several noteworthy advancements in the field of BMS include
Intelligent BMS
BMS can enhance battery efficiency based on usage patterns, environmental factors, and other dynamic circumstances by utilizing sophisticated algorithms and machine learning approaches. Automakers benefit from this technology since it lowers warranty claims and improves their reputation for dependability.
Advanced Predictive Algorithms
Advanced predictive maintenance systems are being linked with battery management systems in electric vehicles. These algorithms use real-time data to predict when battery components would need to be replaced or repaired. By doing so, they lower maintenance costs for customers, increase vehicle dependability, and improve brand reputation.
External Communication
With BMS, wireless communication methods are being used more and more, allowing for quick system upgrades via Over-the-Air (OTA) updates. Automotive OEMs can maintain the functionality and performance of their BMS in the interim by applying updates on schedule.
Key Players of BMS industry
- Leclanche
- ST Microelectronics
- Robert Bosch GmbH
- Sensata Technologies
- Maxwell Energy Systems
- Toshiba Corporation
- Panasonic Corporation
- Midtronics Inc.
- Deutz AG
- Nuvation
- Eberspächer
- Texas Instruments Inc.
- Elithion Inc.
- Hero Electric
Recent Developments
In May 2023, targeting low-voltage electric vehicles and energy storage systems, Sensata's c-BMS24X BMS offers enhanced software features to enhance vehicle range, uptime, and battery health/performance. Convenience features including automated sleep mode, flexible design, and the ability to connect up to 10 battery packs in parallel for enhanced safety are all included in the system. Additionally, it provides battery switch functionality, better energy, health, and state of charge prediction and measurement, as well as improved balance for cell chemistries such as lithium iron phosphate (LFP). Sensata intends to introduce the technology in Stuttgart, Germany at The Battery Show.
In January 2023, Hero Electric and Maxwell Energy Systems have established a long-term collaboration for sophisticated battery management systems. Hero Electric will receive 10 lakh units of Maxwell's BMS during the course of the following three years. Through the collaboration, Hero Electric will be able to provide its clients safe, high-performing EVs, establish a domestic supply chain, further the goals of Made in India, and lessen its reliance on imports. Hero Electric's e2W series is among the several chemistries and configurations that Maxwell's automotive-safe BMS supports. For the Indian EV market, the two partners will create a new line of cutting-edge electrical items.
About the Spherical Insights & Consulting
Spherical Insights & Consulting is a market research and consulting firm which provides actionable market research study, quantitative forecasting and trends analysis provides forward-looking insight especially designed for decision makers and aids ROI.
Which is catering to different industry such as financial sectors, industrial sectors, government organizations, universities, non-profits and corporations. The company's mission is to work with businesses to achieve business objectives and maintain strategic improvements.
CONTACT US:
For More Information on Your Target Market, Please Contact Us Below:
Phone: +1 303 800 4326 (the U.S.)
Phone: +91 90289 24100 (APAC)
Email: inquiry@sphericalinsights.com, sales@sphericalinsights.com
Contact Us: https://www.sphericalinsights.com/contact-us
Need help to buy this report?